Standard operating procedures (SOPs) ensure that technicians perform and complete assigned tasks correctly, efficiently, and cost effectively every time. Without foolproof procedures in place, different employees will execute assignments in different ways, for better or worse!
Every company needs organizational systems to manage business processes.
When it comes to maintenance departments, one of the most essential SOPs an organization can create is a system for work order management because equipment reliability is crucial for success in today’s global economy. In fact, we believe work order systems are the backbone of reliable business operations.
Depending on the size of their facilities, maintenance managers likely manage multiple work orders simultaneously. If you’re in this position, improper management puts you at risk of inefficiency and wasted resources.
Successful work order management (and, by extension, maintenance management) requires you to know how to prioritize, account for the resources they have, and know how to allocate these resources.
You’ll also need a well-trained and empowered workforce ready and able to utilize the systems you have in place. Most of all, you’ll need the right tools to execute the plan you come up with. The right software will simplify the system and its processes, helping you manage multiple work orders, track their end-to-end progress, gain insights into your teams’ past and present performance, and apply these insights to optimize your work order management, all of which will bolster your overall maintenance strategy.
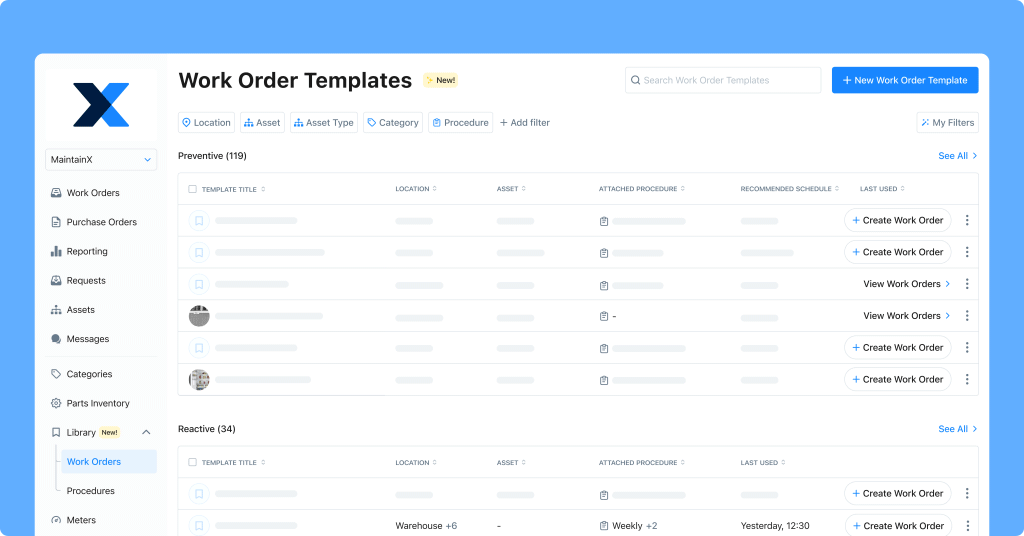
The Work Order Process
In general, a successful work order process consists of the following steps:
- Creating a Work Request
- Creating the Work Order
- Carrying Out the Task
- Completing the Work Order
- Reviewing the Process
The success of each of these steps depends on instituting proper systems to answer fundamental questions. For example,
- Should team members respond to every problem by creating work requests?
- If not, how do they know what issues to create work requests for?
- Beyond that, should maintenance managers approve all work orders simultaneously? If you’ve ever been in this position, your answer is probably, of course not. But how to know which work orders have priority?
- Similarly, who gets assigned to what task?
- How do managers track the progress of a work order?
Clear answers to these questions will help you create a work order management system that works.
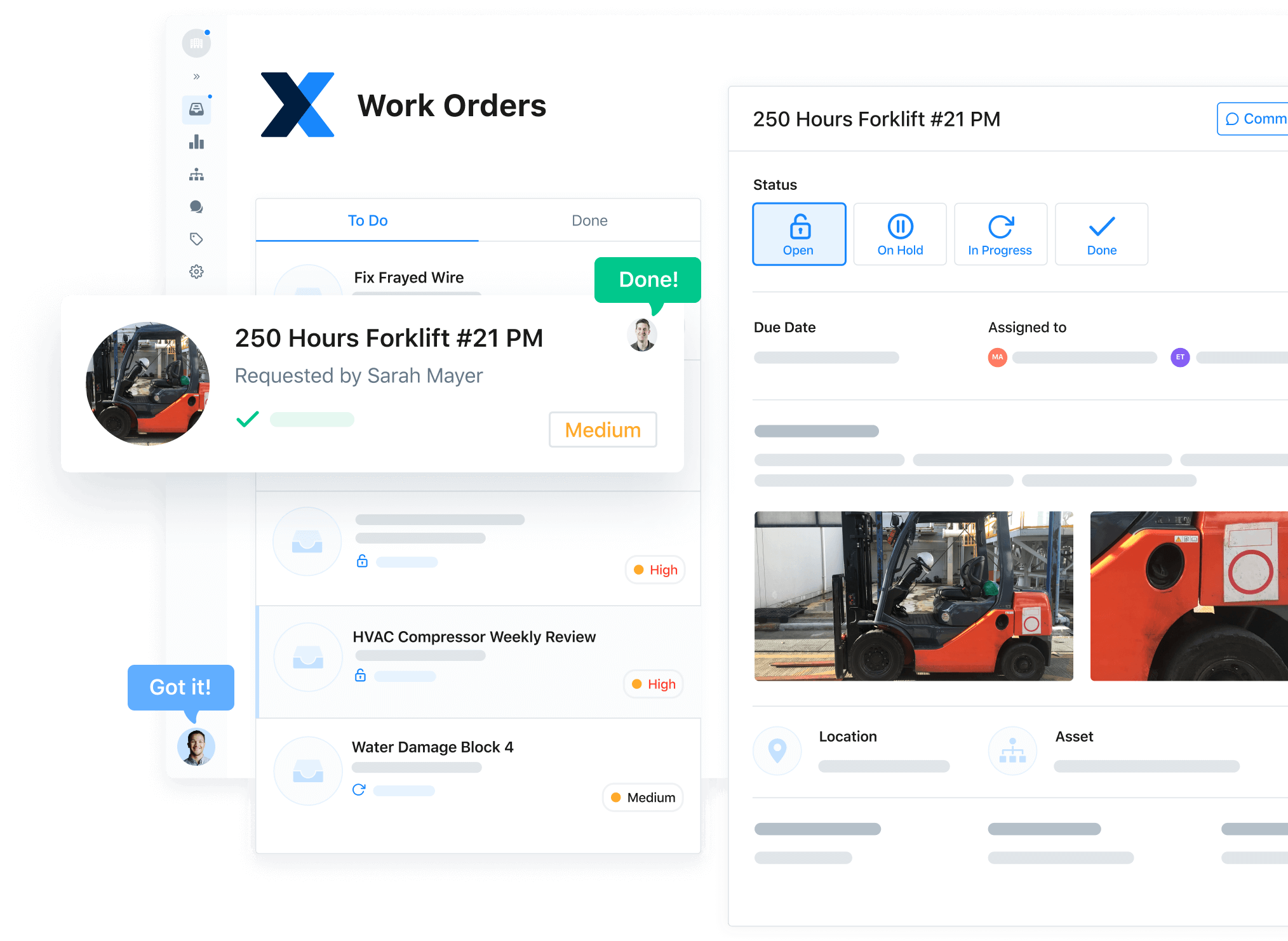
How to Create a Work Order System
High maintenance-task volume requires organized work order management systems. A work order system is a documented process to assign, complete, and document operational and maintenance activities according to organizational standards. The benefits of instituting a robust work order management system in your facility include the following:
- Establishing standards for your operating and maintenance processes
- Ensuring staff carry out tasks properly to reduce human error
- Tracking work orders: from work request to completion
- Managing asset and parts inventory so you have the necessary parts to maintain your assets
- Maintaining regulatory compliance
Without streamlined processes in place, your business may suffer from decreased productivity, time-consuming miscommunication, and costly technician errors.
Eight Steps to Creating a Work Order Management Process
1. Understand and Implement the Right Maintenance Plan
Technically speaking, maintenance work orders fall into three primary workflows: recurring planned work orders, planned work orders, and unplanned work orders.
Maintenance managers select workflows to execute the appropriate maintenance strategies as per machine, location, priority, cost, etc. The more complex pieces of equipment under a maintenance department’s care, the more likely a combination of maintenance strategies keeps the equipment running in optimal condition.
The four primary types of maintenance are:
Preventive Maintenance (PM)
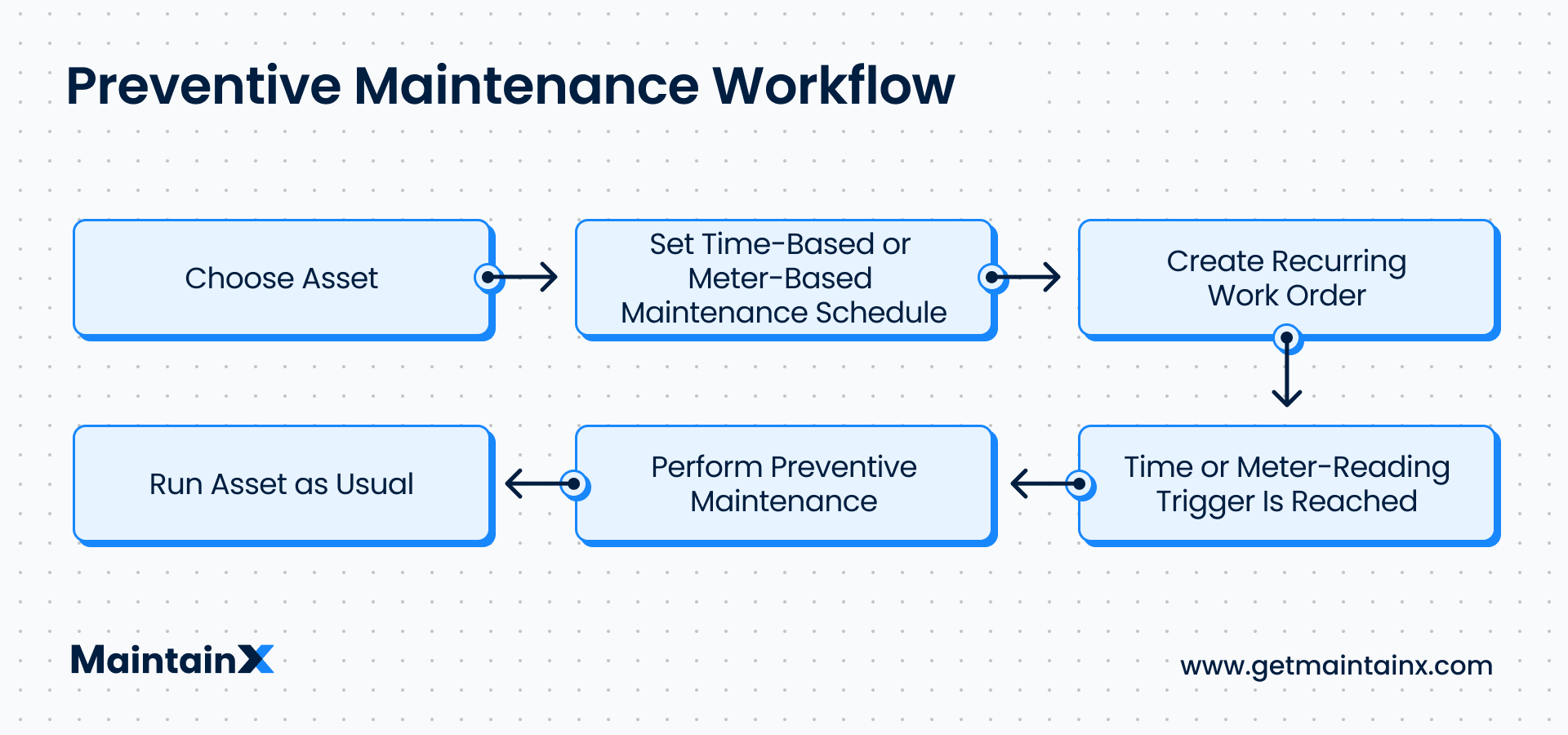
Preventive Maintenance (PM), also called scheduled maintenance, refers to planned maintenance that prolongs the lifespan of company assets, equipment, and infrastructure. Everyday PM tasks include adjusting, cleaning, lubricating, repairing, and replacing equipment parts.
Predictive Maintenance (PdM)
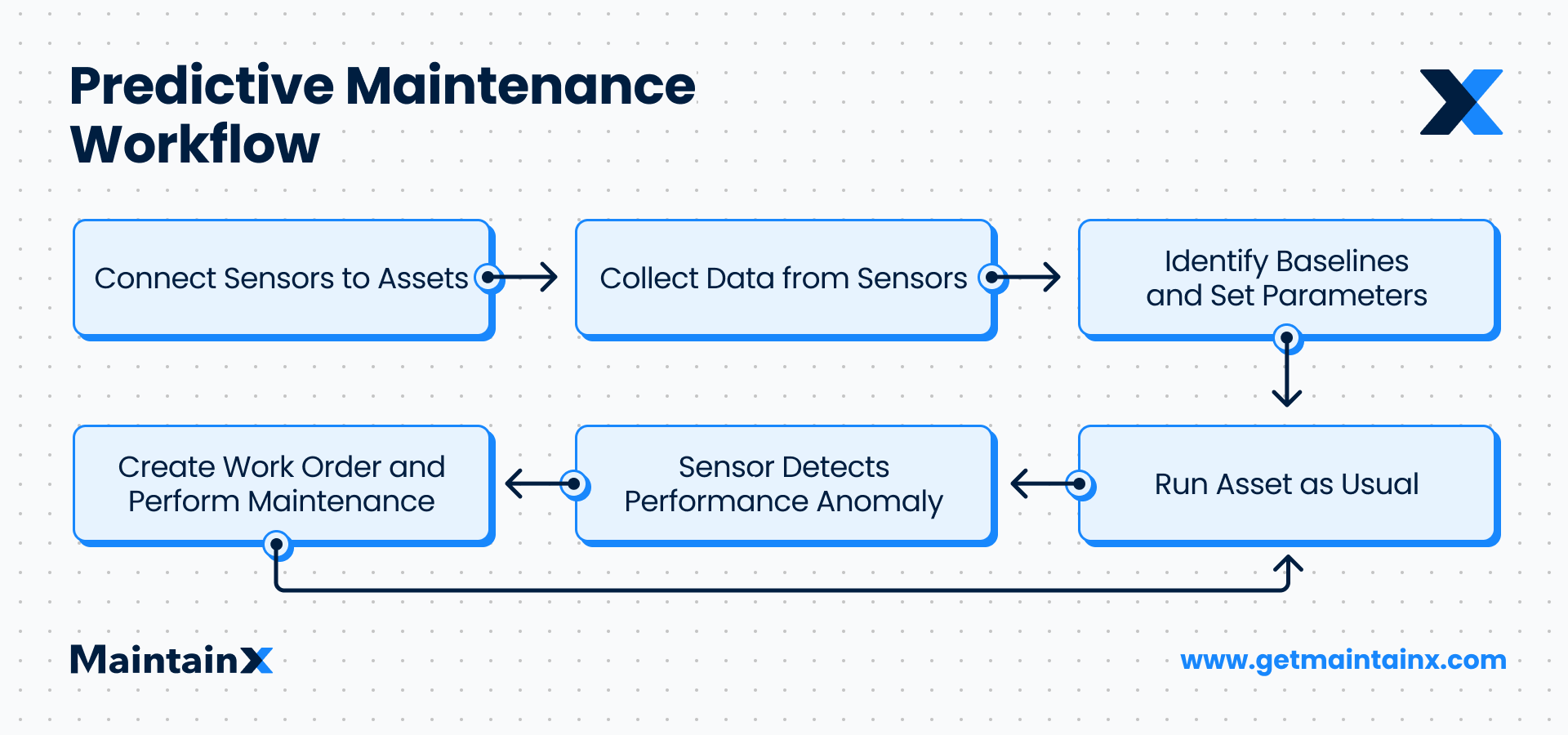
Predictive maintenance (PdM) is an advanced form of preventive maintenance that relies on machine learning technologies to establish baseline patterns of “normal equipment operations.” These metrics are then combined with complex algorithms to predict future behavioral issues and schedule PdM tasks at optimized dates. IoT (Internet of Things) technology can gather equipment data to predict breakdowns. As managing this data is key to the success of a predictive maintenance program, it’s vital to find the right tools.
A CMMS with functionality for asset tracking and data management can make the difference between regularly maintaining equipment and emergency troubleshooting during emergencies. Vibrational analysis, acoustic analysis, and infrared analysis are the primary types of PdM technologies used by leading maintenance departments.
Condition-Based Maintenance (CBM)
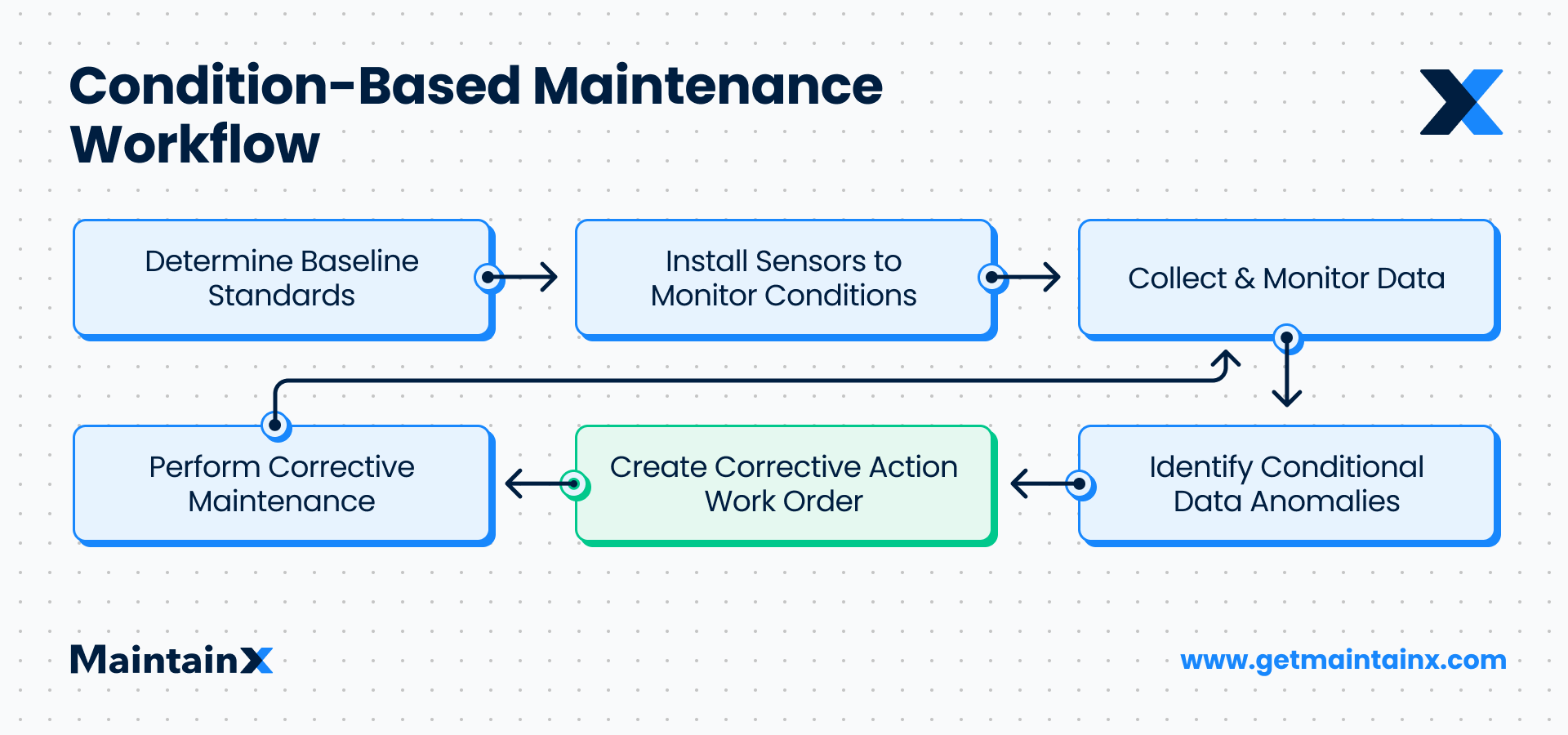
Condition-based maintenance (CbM)uses devices, sensors, and scheduled tests to measure real-time equipment behavior. When assets approach pre-defined qualifications for maintenance, installed sensors trigger automated work orders via CMMS. As the workflow in the diagram shows, central to CbM is data collection and monitoring. Equally vital are identifying data anomalies and scheduling corrective actions. Collecting and monitoring data requires technology that teams can integrate with their asset monitoring protocols. In addition, to identify anomalies, teams need to be able to track data over time to establish consistent baselines and identify trends. As such, look for work order software that already provides data visualization and other robust reporting features.
Corrective Maintenance (CM)

Corrective maintenance (CM) is a type of maintenance that restores assets to working condition after they have broken down. CM includes troubleshooting, disassembling, readjusting, repairing, replacing, and realigning equipment. Workers will often request or assign unplanned maintenance in the form of a work request or emergency phone call. With the right CMMS app, this also can be done via instant chat, which can save time in an emergency. Work order software with group chat functionality also facilitates collaborative troubleshooting.
Most small- to medium-sized businesses (SMBs) combine preventive and reactive maintenance, while larger organizations with many expensive assets are more likely to incorporate PdM and CbM technologies into their maintenance programs.
Check out the section “How to Build a Maintenance Strategy” to match assets with maintenance strategies.
2. Evaluate Paper vs. Digital Work Order Methods
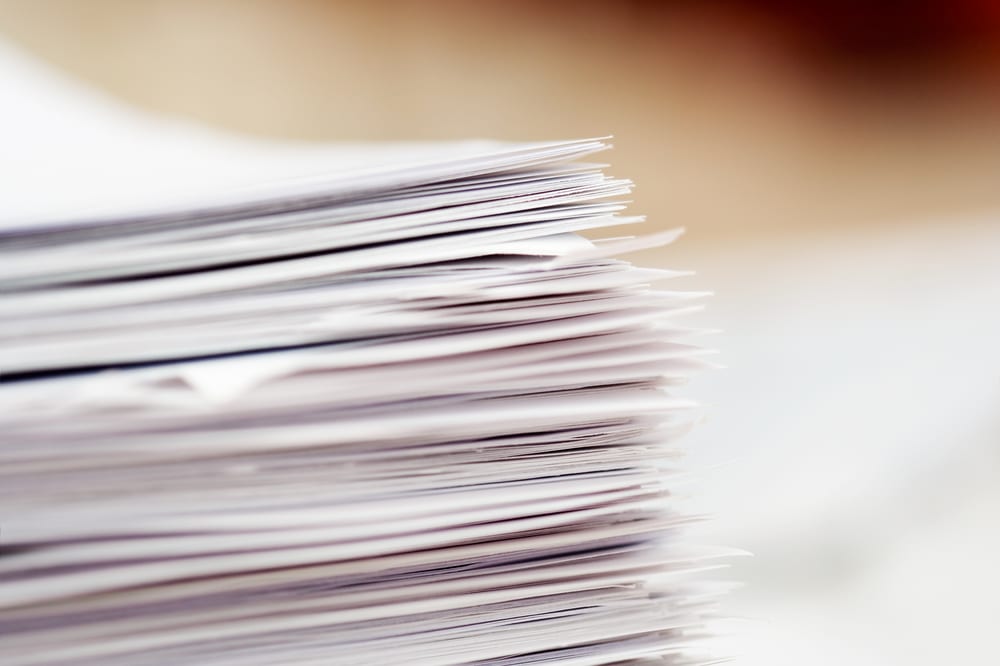
Once you’ve identified your organization’s ideal maintenance strategies, consider how you will create, distribute, and monitor the work orders. You have two primary options: paper work orders or digital work orders.
Paper work orders are what they sound like sheets of paper that include important instructions for performing assigned maintenance tasks. Most paper work orders include an asset’s name, location, and instructions to complete the task at hand. Of course, writing recurring work orders by hand is a time-consuming process. The more equipment you’re responsible for maintaining, the more tedious paper work orders can become. Not to mention that paper work order books don't allow for easy filing based on assets, parts, or location information.
Alternatively, digital work orders are what they sound like—work orders created digitally using software. Managers commonly create digital work orders using spreadsheets, online forms, free work order generators, or computerized maintenance management systems (CMMS).
While digital work orders provide plenty of benefits—increased flexibility, convenience, and transparency—their most noteworthy one is saved time and money, along with an easy store of history. In the event of issues, digital work orders provide robust audit trails that are a good place to begin troubleshooting.
The good news is that today’s cloud-based work order software programs are available for nominal monthly fees, and some providers offer free versions with substantial functionalities.
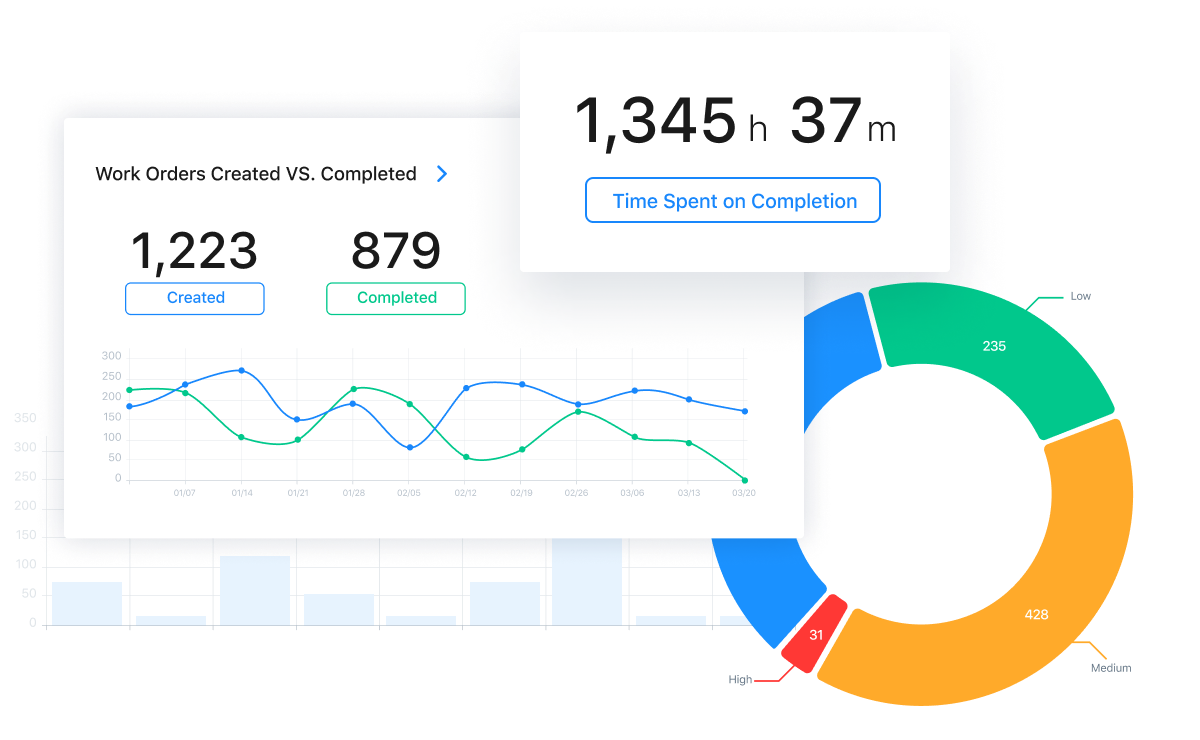
Three Reasons to Go Digital
First, paper work orders are more likely to result in lost data. Besides the risk of losing historical records, misplaced work orders can complicate auditing processes.
Second, busy organizations misplace 7% of paper documents. Alternatively, digital work orders stored in cloud-based software eliminate the chance of losing paper trails entirely.
Third, companies spend nearly 75% of their time using paper work orders to search for and file work orders. Conversely, employees using CMMS can quickly access organized digital work orders via smartphone. In fact, studies show that work order software can improve time management by 40% by allowing deskless workers to access work orders directly from mobile devices.
In other words, digital work orders provide several key advantages that CMMS can optimize even further. Luckily, the best work order programs today offer mobile applications with full functionality.
3. Implement CMMS Software
Your next step is to choose a method to create, assign, and track your digital work orders. MaintainX is a work order software provider. and therefore, it should come as no surprise that we recommend implementing a CMMS if you want to create effective work orders. The software has flexible scheduling features that allow managers to review work history, track assets, and document maintenance work. Such capabilities are advantageous when repairing equipment malfunctions as efficiently as possible. Here’s a quick look at a MaintainX dashboard:
In addition to work order management, modern desktop and mobile CMMS applications allow users to collect, segment, filter, and analyze detailed O&M data points. App users can search for information via vendor, asset, location, parts, scheduled technician, and more. Translation: No more time wasted hunting down sparse and incomplete details stored in dusty old filing cabinets.
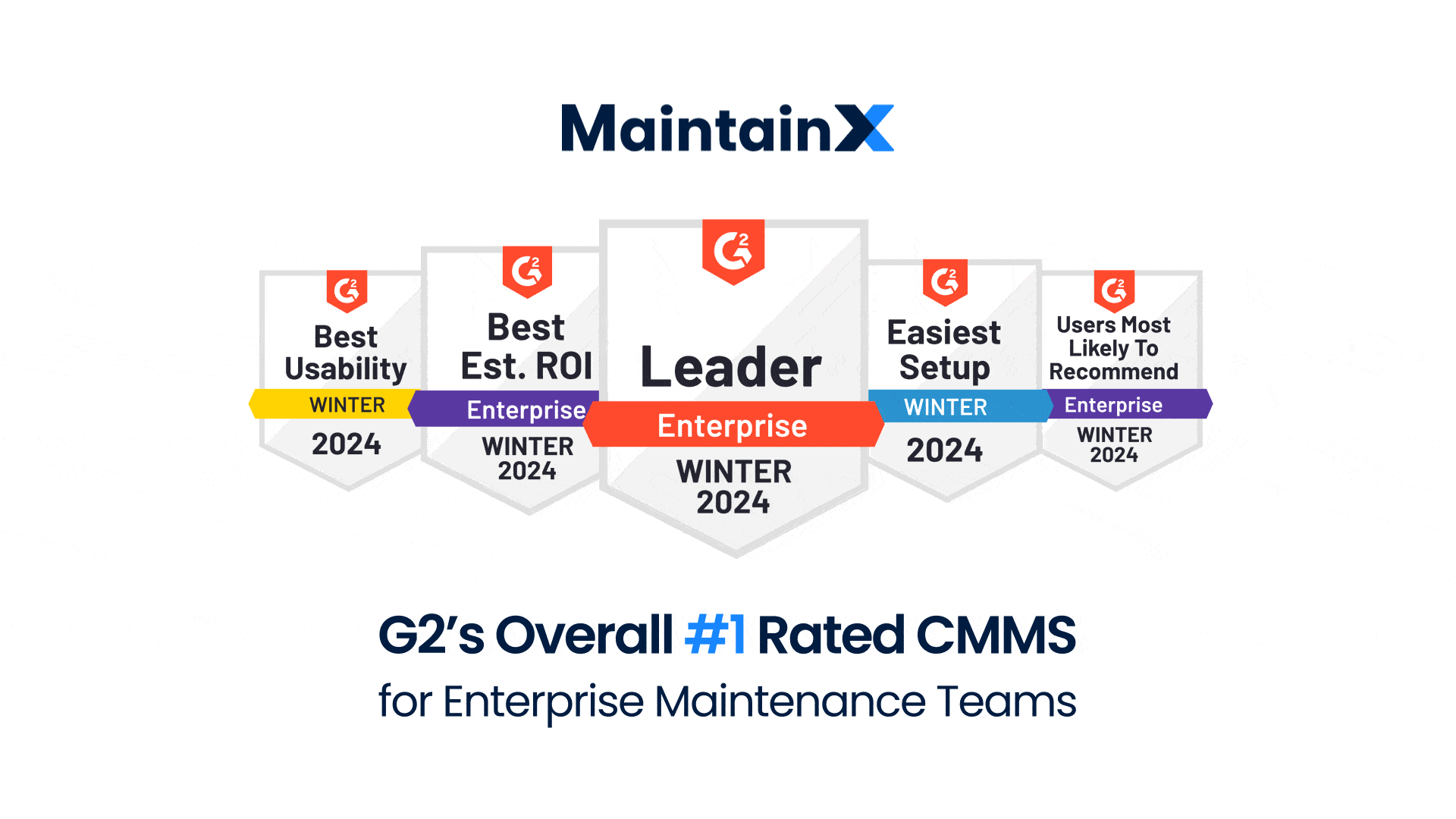
With MaintainX, for example, managers can instantly pull up the maintenance history of essential company assets upon request. And, a technician can use the software to compile manufacturer-requested historical information for warranty equipment and parts fulfillment.
Depending on an organization’s size and the number of assets, technicians can find it challenging to remember which assets the maintenance team last worked on and when. Digitized work orders can provide notes about repair histories, troubleshooting, and standard operating procedures.
CMMS with robust reporting features help operational managers track key performance indicators and metrics like Mean Time to Repair (MTTR), Planned Maintenance Percentage (PMP), and Scheduled Maintenance Critical Percentage (SMCP). Such key performance indicators (KPIs), along with worker time and cost tracking, can provide deeper insights for improving facility maintenance programs.
4. Create Work Orders for All Tasks
Some companies only use digital work orders for significant maintenance assignments. But we suggest creating work orders for tasks both large and small. Doing so will help your organization compile complete historical records to inform optimal maintenance scheduling, parts ordering, and maintenance team assignments.
For example, if a particular part consistently requires replacement, you may decide to increase the number of spares kept on hand. This way, your team can avoid the expedited shipping costs associated with ordering emergency parts and prolonged downtime waiting for the part to arrive. Your work order software’s inventory modules are critical here. Look for software that features third-party vendor integration. MaintainX, for example, can trigger purchase orders automatically and send these to vendors who are not on MaintainX.
Alternatively, your CMMS advanced reporting dashboard data may indicate a particular asset’s Useful Life has expired. In other words, your organization would save more money in the long run by purchasing a completely new piece of equipment instead of performing frequent maintenance on an old asset. Plant Engineering reported that 40 percent of unplanned downtime is due to aging equipment.
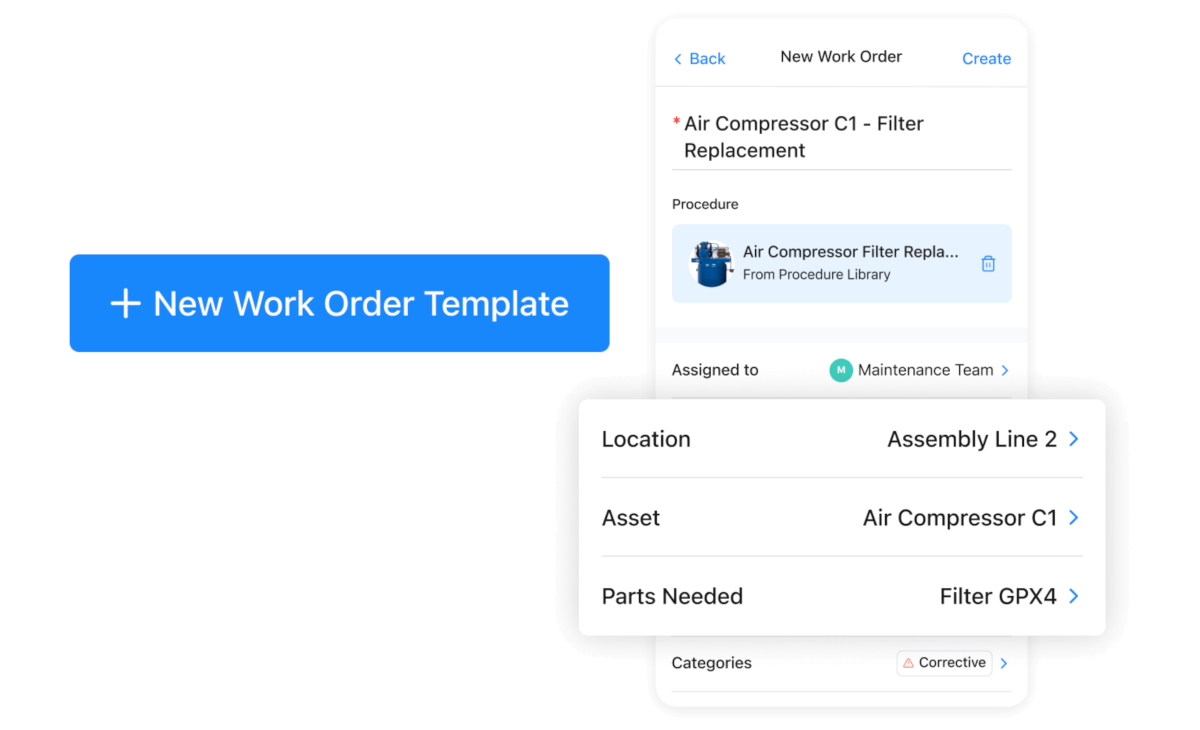
5. Use SOP Templates
With a CMMS, you don't need to know how to write a work order from scratch. You can duplicate and expand even the most complex work orders with attached Standard Operating Procedure (SOP) templates. The accompanying checklists help reduce human error by outlining clear protocols to follow.
SOPs also help improve adherence to quality control, safety, and efficiency standards. The best procedural templates include form field options, like pass/fail, multiple choice, and checkboxes. MaintainX offers SOP templates across operational use cases, housed in a Global Procedure Library that also contains industry-specific checklists, manuals, and other valuable resources.
Users can also attach work instructions, manuals, photos, and illustrations to provide more detailed support.
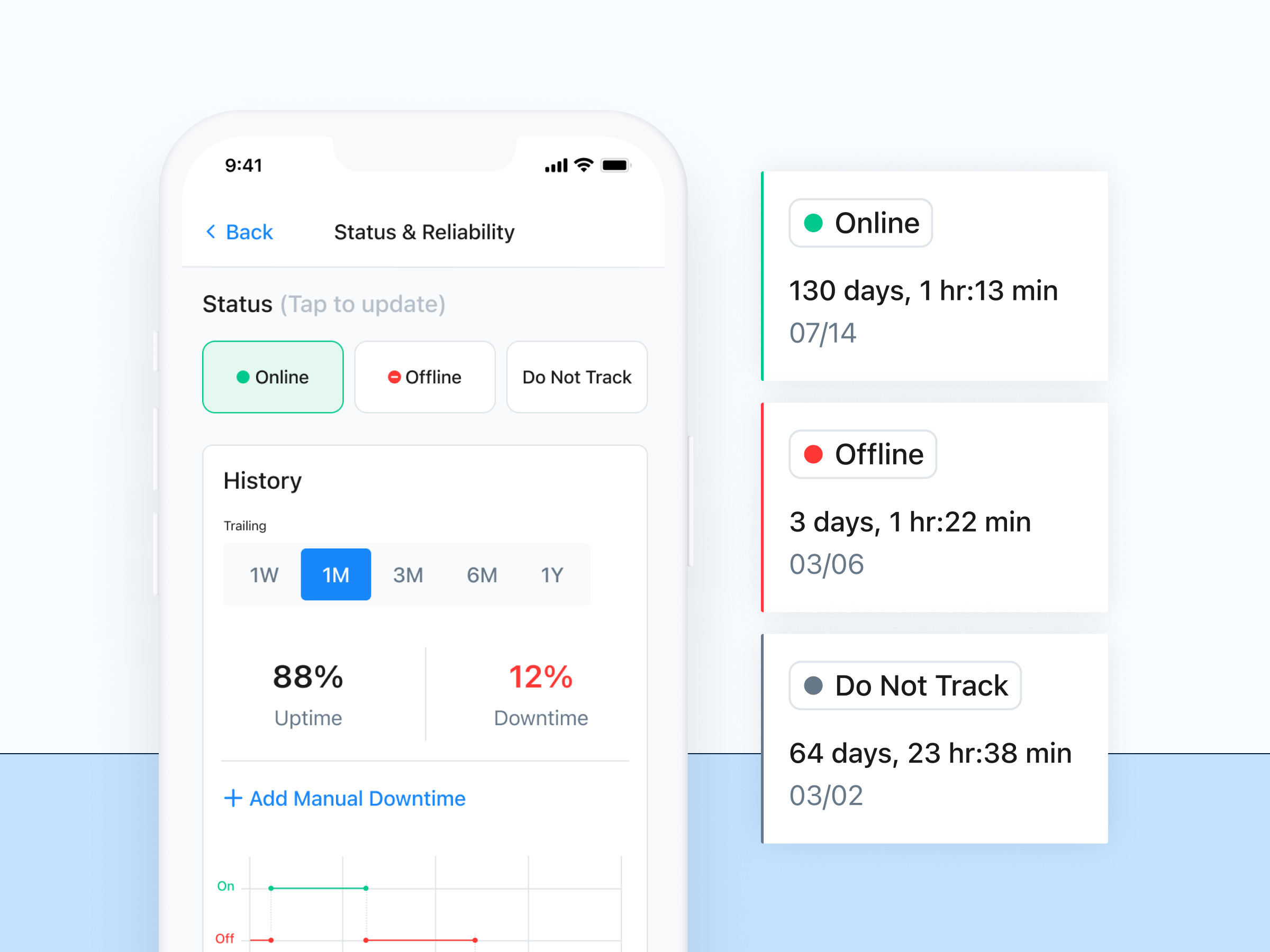
6. Prioritize Work Orders
Undoubtedly, organizing maintenance tasks with digital work orders simplifies O&M management. And savvy operational managers take things further by prioritizing work orders based on criticality analysis and competing needs. Establishing an asset hierarchy to prioritize tasks is especially important for industrial manufacturers relying on complex machinery.
In such instances, unplanned downtime losses can cost a company thousands of dollars for every minute a critical piece of equipment is down. The International Society of Automation (ISA) reports the average factory loses 5 percent of its productive capacity and takes up to a 20 percent loss because of downtime. A manufacturer’s bottom line can include a whopping 800 hours of downtime, translating into millions of dollars of lost revenue!
These days, maintenance teams are often understaffed, and considering not all equipment is equally important, management needs to maximize available resources. With the right work order software, you can assign priority labels to work orders based on criteria of your own making. You can also refine your priority matrix based on our reporting dashboard's key performance indicators.
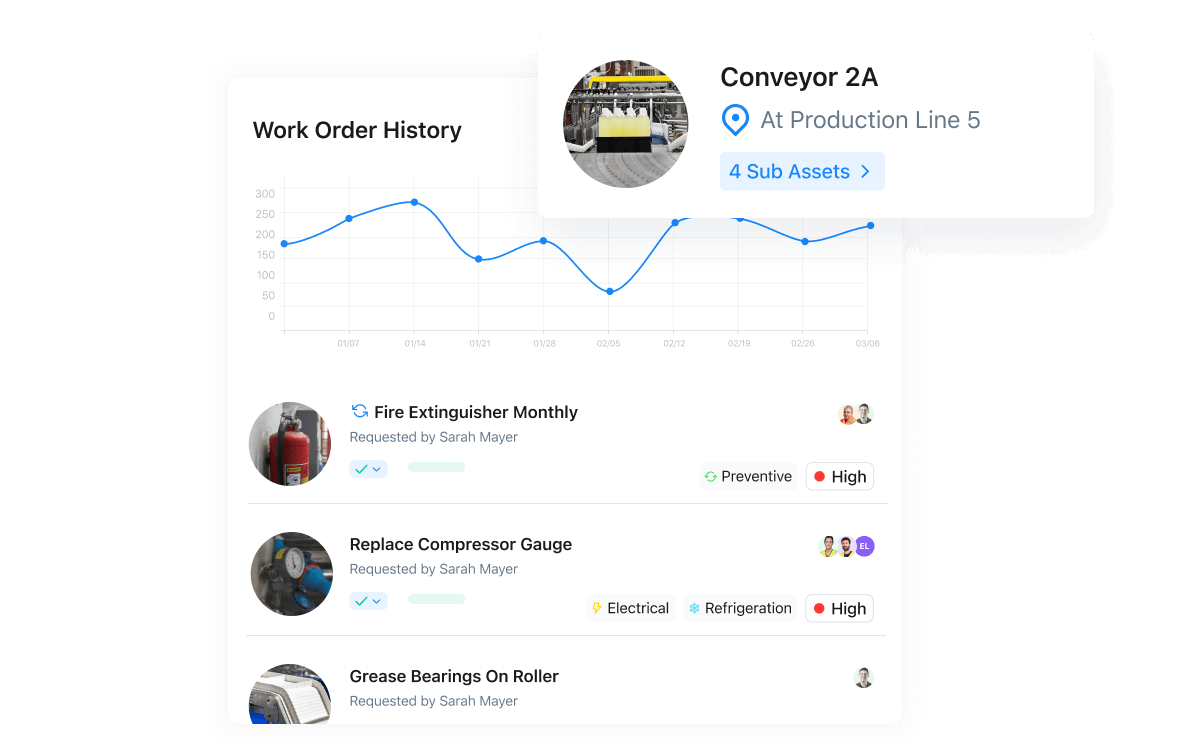
7. Automate Work Orders for Recurring PMs
Creating a digital work order system means you don’t need to assign recurring tasks manually. While most CMMS can easily handle unplanned maintenance work orders, the best work order management software shines most when it comes to scheduling PM tasks.
Examples of using triggers to automate work orders include:
- A storage tank is above safe capacity
- A temperature reading is below a safe threshold
- A vehicle reaches 5,000 miles of use
Management can set repeating work orders for daily, weekly, or monthly intervals. Managers can also automate PMs according to usage triggers. For example, MaintainX’s Meters feature allows maintenance teams to track odometer readings, engine run times, cycle counts, and more.
8. Develop a Work Order Review Process
Finally, create a management system to review your work orders and the process itself. Choose key performance indicators (KPIs) to help advance your company’s maintenance goals. At a minimum, calculate your monthly planned maintenance percentage (PMP).
PMP measures the number of planned maintenance tasks compared to all maintenance tasks. Then, based on the PMP, determine where you need to make improvements.
Earlier, we mentioned the importance of choosing work order software with a robust reporting module. MaintainX’s Reporting features allow you to review your processes, identify potential areas to improve, and produce actionable insights. Save time on administrative reporting with custom dashboards, optimize your financial management with cost tracking, and improve safety by identifying where and when incidents are most likely to occur.
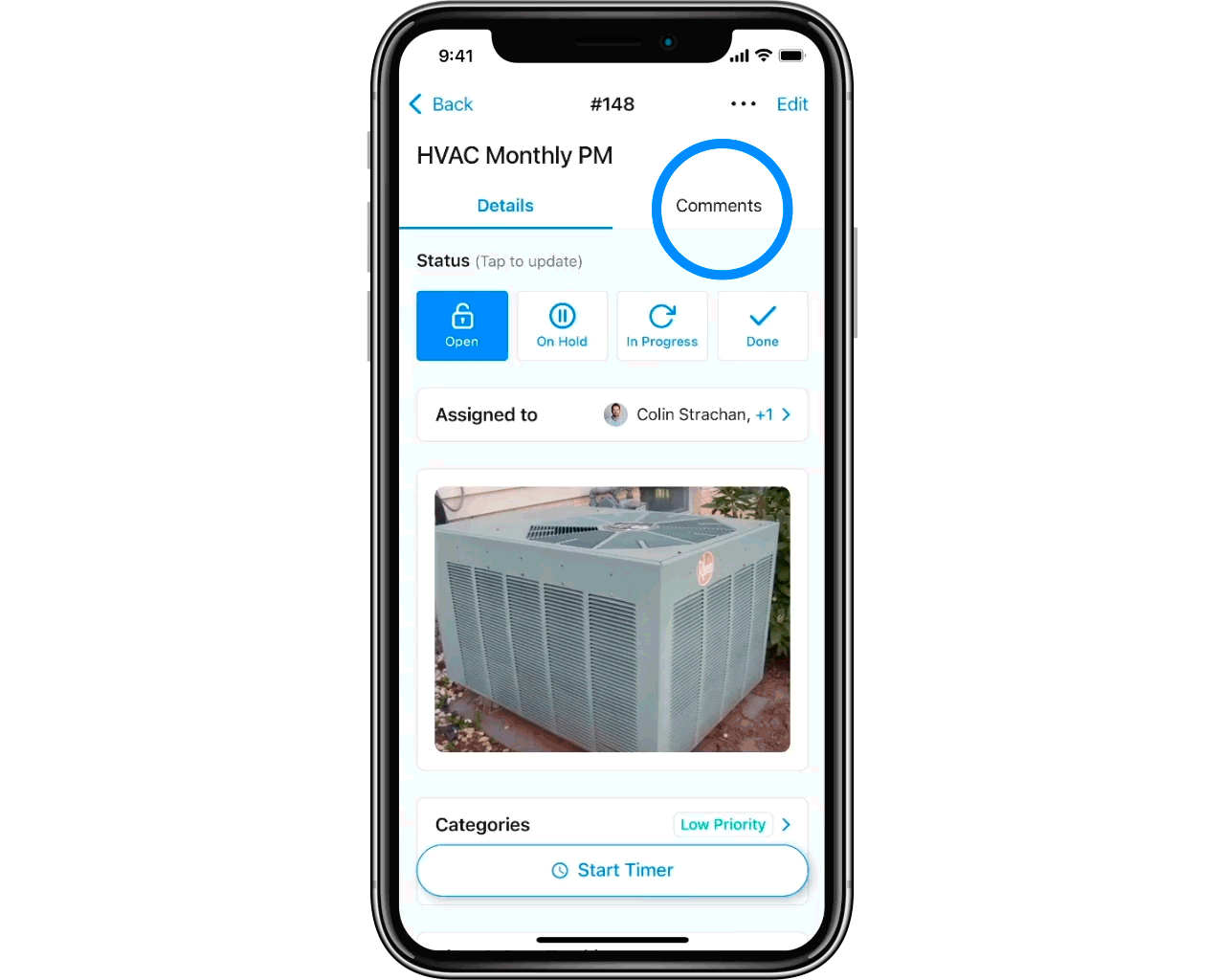
Get MaintainX Work Order Management Software Today
Regardless of industry, work order software is hands down the most effective way to create, assign, and manage maintenance assignments. MaintainX helps simplify work order management for operational managers and maintenance technicians by:
- Standardizing Processes: A Computerized Maintenance Management System (CMMS) enables you to streamline your workflows by allowing you to create standards for maintenance work. You can organize routine tasks into step-by-step processes that are easy to follow. Standardization is also helpful for asset management, facility management, and inventory management.
- Providing Advanced Reporting: Customized dashboards all you to monitor and report on performance metrics that matter most to you and your team. Dashboards can help increase uptime, team efficiency, and compliance, including identifying the team with the lowest PM compliance rate, spotting skipped tasks to uncover issues with the work order process, and discovering which critical assets cost you the most.
- Streamlining Communication: Provides work order commenting, team messaging, and individual messaging thread options for real-time communication. Team members can chat directly from the MaintainX app and check in on tasks in progress.
- Ensuring Accuracy of Work: With the right CMMS, you can include instructions in your work order details. A work order template with checklists helps ensure staff complete tasks precisely as they should, forgetting no steps. MaintainX also comes with a Global Procedure Library with SOPs across industries and equipment types.
- Facilitating Real-Time Monitoring: With CMMS software, maintenance managers can view all open, in-progress, and closed work orders with the click of a button. They can monitor work orders from work order ticket creation to completion.
- Managing Inventory and Parts: A robust work order management system lets management conveniently track available equipment parts crucial to ongoing facility operations. Use QR codes and barcodes for easy inventory access and take advantage of MaintainX’s purchase orders feature with third-party vendor integration. This app feature allows users to trigger purchase orders automatically to vendors outside the system.
- Maintaining Regulatory Compliance: With CMMS solutions, you can automate your regulatory efforts by setting due dates and repeatability settings to get alerts when inspections are upcoming. Instead of relying on memory to complete compliance tasks, make them part of your routine maintenance. Maintain regulatory compliance with a full inspection history at your fingertips. Your team will be prepared for an unannounced visit from an inspector.
- Simplifying Invoicing: Managers can convert digital work orders to PDFs to email with attached invoices. Also, MaintainX integrates with over 4000+ software apps, connecting your maintenance work with departments across your organization.
Want to understand why McDonald’s, Titan America, and Duracell all manage their work order systems with MaintainX?
FAQs
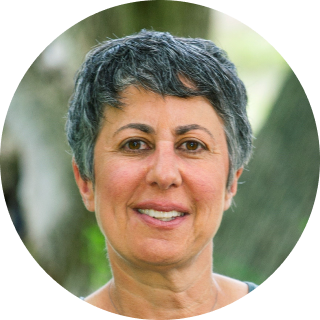
Caroline Eisner
Caroline Eisner is a writer and editor with experience across the profit and nonprofit sectors, government, education, and financial organizations. She has held leadership positions in K16 institutions and has led large-scale digital projects, interactive websites, and a business writing consultancy.